
高效加工新选择:多槽型可转位刀片
刀具金属加工行业的挑战与机遇近年来,随着制造业向智能化、高效化方向转型,金属加工领域对刀具性能的要求日益严苛。传统单一槽型刀具已难以应对多样化加工需求——粗加工需要高强度的刃口承载能力,半精加工则要求精准的切屑控制与表面光洁度。此外,能源成本上升、材料复杂度增加(如高强度钢、钛合金的广泛应用)以及环保法规的收紧,进一步倒逼企业寻求更高效、更耐用的刀具解决方案。在此背景下,多槽型可转位刀片应运而生。其通过差异化的几何设计、材料优化及场景适配性,成为现代金属加工中不可或缺的“智能工具”。无论是汽车制造中的重载切削,还是航空航天领域的精密加工,多槽型刀片均能通过灵活切换槽型,显著提升加工效率并降低成本。作为长期深耕机械加工配套服务的箭穿石,在该类刀具的现场推广与应用实践中积累了丰富经验,已成功协助众多客户优化切削方案、提升产线效率。
关键词:
所属分类:
产品描述
关键词:多槽型刀片 可转位刀具 高效金属加工 粗精加工刀具
近年来,随着制造业向智能化、高效化方向转型,金属加工领域对刀具性能的要求日益严苛。传统单一槽型刀具已难以应对多样化加工需求——粗加工需要高强度的刃口承载能力,半精加工则要求精准的切屑控制与表面光洁度。此外,能源成本上升、材料复杂度增加(如高强度钢、钛合金的广泛应用)以及环保法规的收紧,进一步倒逼企业寻求更高效、更耐用的刀具解决方案。
在此背景下,多槽型可转位刀片应运而生。其通过差异化的几何设计、材料优化及场景适配性,成为现代金属加工中不可或缺的“智能工具”。无论是汽车制造中的重载切削,还是航空航天领域的精密加工,多槽型刀片均能通过灵活切换槽型,显著提升加工效率并降低成本。
作为长期深耕机械加工配套服务的箭穿石,在该类刀具的现场推广与应用实践中积累了丰富经验,已成功协助众多客户优化切削方案、提升产线效率。
一、核心技术解析:三大槽型设计的科学逻辑
1. A型槽:粗加工场景的高效解决方案
结构设计:
正前角切削刃:通过增大前角(典型值15°-20°),降低切削阻力,减少机床负载。
强化刃口设计:采用圆弧过渡刃口与微米级涂层技术(如TiAlN涂层),提升抗崩损能力。
宽排屑槽:加宽排屑槽空间,避免切屑堆积导致的二次切削损伤。
材料科学:
刀片基体采用超细晶粒硬质合金(WC-Co基),晶粒度控制在0.5μm以下,确保高硬度的同时兼顾韧性。表面通过化学气相沉积(CVD)工艺复合涂层,形成耐磨层(Al₂O₃)与润滑层(TiN)的双重保护。
应用场景:
典型加工参数:进给量0.20-0.60mm/r,切深1.0-6.0mm,线速度80-150m/min。
适用领域:重型机械部件(如风电齿轮箱、工程液压阀体)的粗开槽、大余量车削。
对比优势:相较于传统负前角刀片,切削力降低20%-30%,加工效率提升15%以上。
2. B型槽:中等加工的均衡之选
结构设计:
变前角设计:切削刃前角从刀尖到后部逐渐增大(10°→25°),平衡切削轻快性与刃口强度。
精密断屑槽:采用阶梯式断屑槽,引导切屑规则卷曲,避免缠绕工件或刀具。
刃口倒棱处理:通过纳米级刃口钝化技术,减少微观崩刃,延长使用寿命。
材料科学:
基体采用梯度硬质合金,从表层到芯部钴含量逐步增加(表层6%→芯部10%),实现表层高耐磨与芯部高韧性的结合。涂层则选用自适应润滑涂层(如MoS₂掺杂TiCN),在高温下释放润滑成分,减少积屑瘤形成。
应用场景:
典型加工参数:进给量0.15-0.55mm/r,切深1.5-6.0mm,线速度120-200m/min。
适用领域:汽车发动机缸体、连杆等批量零件的半精加工,兼顾效率与表面质量。
对比优势:在同等切削参数下,刀具寿命较传统刀片延长30%-40%,换刀频率降低50%。
3. C型槽:通用加工的灵活选择
结构设计:
断屑槽延伸至切削刃:通过几何仿真优化断屑槽轨迹,确保小切深(0.5mm)时切屑有效断裂。
双曲面排屑通道:采用3D曲面排屑设计,增强大切深时的卷屑压力,避免长切屑划伤工件表面。
微织构刃口:在切削刃表面激光雕刻微米级沟槽,降低切削热积聚,提升加工稳定性。
材料科学:
基体采用纳米复合陶瓷(Si₃N₄基),硬度可达HRA93,同时具备优异的高温抗氧化性(耐温1200℃)。涂层方案选用多层梯度结构(TiAlN/AlCrN交替沉积),兼顾耐磨性与抗热震性能。
应用场景:
典型加工参数:进给量0.12-0.60mm/r,切深0.5-5.0mm,线速度150-300m/min。
适用领域:航空航天薄壁件、医疗器械精密零件的半精加工及仿形切削。
对比优势:在铝合金加工中,表面粗糙度可达Ra0.4μm,较普通刀片提升50%。
二、产品核心价值:从设计到应用的全链路优化
1. 材质升级
粉末冶金工艺实现HRA92-94的硬度与4000MPa抗弯强度
PVD+CVD涂层厚度3-8μm,显微硬度>HV3000
ISO 3685验证:连续加工100分钟后VB≤0.2mm
2. 场景覆盖
粗加工:A型槽,耐冲击、排屑顺畅
中等加工:B型槽,平衡耐用与断屑
半精加工:C型槽,追求尺寸与表面一致性
箭穿石在上述应用场景中,结合客户机床结构、夹具方案与冷却方式,协助制定最优刀具搭配策略,实现快速切换、最大兼容。
3. 成本优化
切削力下降10%-15%,设备负载减轻
单刃寿命延长30%-50%,平均刀具成本下降
干式/微量润滑适配,降低切削液使用量,符合绿色制造趋势
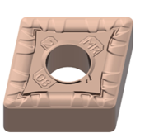
三、行业应用案例:数据驱动的效率革命
案例1:汽车传动轴高效粗加工
客户痛点:传统刀片寿命仅80分钟,频繁换刀影响产能
解决方案:采用A型槽刀片,线速度130m/min,切深5.0mm
成果:单刃寿命提升至150分钟,月产能+22%,成本下降18%
箭穿石在该项目中提供选型与加工参数建议,帮助客户完成切削路径优化。
案例2:航空钛合金薄壁件精密加工
客户痛点:表面粗糙度波动大,Ra0.8-1.6μm,废品率高达12%
解决方案:更换C型槽刀片,进给量0.20mm/r,使用高压气雾冷却
成果:Ra稳定在0.4-0.6μm,废品率降至3%,年节省材料费200万元
箭穿石与客户共同完成多轮冷却策略与切屑排布的仿真与试验。
案例3:模具钢型腔断屑改善
客户痛点:Cr12MoV材料切屑缠绕,停机频繁
解决方案:采用B型槽刀片,切深3mm,进给0.35mm/r
成果:切屑长度由150mm降至20mm以内,日加工时长+4小时
箭穿石在现地调研后,快速制定断屑槽匹配刀具方案,客户反馈良好。
四、未来展望:智能化与定制化趋势
随着工业4.0逐步渗透制造各环节,多槽型刀片将与数字加工系统深度融合:
智能刀柄:嵌入传感器,监测温度/力变化
云端参数匹配:依据材料与机床配置智能推荐槽型/进给组合
定制化涂层平台:为客户提供面向Inconel、碳纤维等特殊材料的专用刀片
箭穿石将继续携手合作伙伴拓展产品服务边界,提升客户切削技术的前瞻性与竞争力。
以技术创新重塑金属加工边界
多槽型可转位刀片不仅是一款功能全面的加工利器,更代表了一种高效、灵活、可持续的加工思维模式。通过科学设计、先进材料与智能适配,它能够满足金属加工多变的挑战场景,实现从效率提升到成本控制的全维突破。
在项目支持与技术导入方面,箭穿石将始终秉持“实用、精准、高效”的理念,持续为制造企业提供值得信赖的技术支援与产品服务,助力客户突破加工瓶颈、创造更大价值。
相关产品
相关案例
欢迎您的留言咨询